CORE SERVICE OFFERINGS
High-Temperature Online Inspection
TCR Engineering provides cutting-edge online inspection solutions designed to minimize plant downtime and reduce costs for operators. With capabilities to perform inspections at temperatures up to 350°C, TCR’s innovations in high-temperature PAUT (HT), ToFD (HT), and corrosion mapping deliver essential data without halting operations. This technique is vital for in-service piping, vessels, and tanks.
Key Benefits of TCR’s High-Temperature Inspection Services:
-
Minimized plant downtime and reduced production losses by conducting inspections online
-
Accurate detection of corrosion, wall thinning, and defect growth for engineering evaluations
-
Real-time corrosion rate monitoring and defect growth tracking for better maintenance planning
-
Supports RBI (Risk-Based Inspection) by delivering critical data for shutdown scheduling
-
Online inspection of repairs, including welds and critical areas, up to 350°C
-
Immediate feedback with digitized inspection records for future reference
-
Enhanced health, safety, and environment (HSE) compliance
By offering in-service inspections, TCR Engineering helps clients avoid costly shutdowns, improve maintenance efficiency, and ensure the safety and reliability of their equipment. Our high-temperature inspection solutions are designed for critical applications, enabling precise and real-time defect detection in the harshest conditions.
High-Temp Phased Array UT



TCR Engineering's high-temperature PAUT inspections are designed to inspect surfaces up to 350°C, minimizing plant downtime. This advanced technique employs sectorial scans that cover the complete weld volume using a range of angles, ensuring comprehensive inspection in even the most challenging environments.
​
-
Suitable for equipment/piping with thicknesses from 3 mm to 300 mm
-
Handles temperatures from 10°C to 350°C
-
Inspects pipelines with diameters of ¾” and above
-
Detects, sizes, and monitors weld defects, corrosion, HTHA, HIC-SWC damage, and stress corrosion cracks
-
Effective for one-sided weld inspections and dissimilar weld joints (CS/SS)
-
Accurate damage/weld defect sizing with high Probability of Detection (POD)
-
Encoded, recordable data/images for detailed analysis
-
Compatible with Inconel and other high-performance materials
-
Enhanced inspection range and cooling capacity via optimized water jacket design
Applicable Standards:
-
ASME Section V (Nondestructive Examination)
-
ASME Section VIII (Pressure Vessels)
-
API 579 (Fitness-for-Service)
-
AWS D1.1 (Structural Welding Code – Steel)
​
TCR Engineering—leading the way in high-temperature phased array inspections, ensuring the safety and integrity of critical infrastructure.
High-Temp Corrosion Mapping
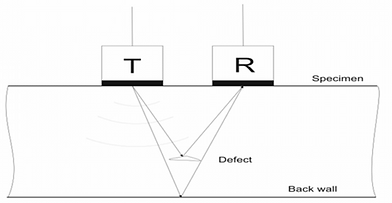

TCR Engineering delivers state-of-the-art automated high-temperature corrosion mapping inspections using the straight beam pulse-echo technique with dual element transducers. Our custom-designed high-temperature probes, crafted from heat-resistant plastics and equipped with advanced cooling systems, ensure reliable performance in extreme environments.
​
-
Suitable for equipment and pipelines with thicknesses from 5 mm to 125 mm
-
Handles temperatures ranging from 10°C to 350°C
-
Effective for pipelines with diameters of 6” and above
-
Accurately detects, sizes, and monitors corrosion, erosion, and HIC-SWC damage
-
Offers precise damage sizing with 0.1 mm accuracy
-
High Probability of Detection (POD) for comprehensive inspection
-
Provides recordable corrosion mapping images for detailed analysis
-
Enhanced inspection angle range and sizing accuracy
​
Our cutting-edge technology ensures accurate, reliable inspections, minimizing downtime and optimizing asset integrity. With advanced probe cooling designs, we deliver highly effective results, even in the harshest environments.
Detecting High-Temperature Hydrogen Attack (HTHA)
TCR Engineering specializes in Advanced NDT services to detect High-Temperature Hydrogen Attack (HTHA), a critical phenomenon in petrochemical and refinery industries. HTHA occurs when steel, exposed to temperatures above 200°C, reacts with hydrogen, creating methane bubbles at the grain boundary. These bubbles lead to microcracks, weakening the steel and potentially causing catastrophic failures.
Even equipment designed under stringent safety codes may suffer from HTHA damage. Early detection through expert NDT inspections by TCR Engineering ensures safe, long-term operation, minimizing risks of equipment failure or accidents.
​
Industries and Equipment at Risk:
-
Catalytic Reformers (CCR & Cyclic)
-
Hydrotreating Units (Hydrocracking and Desulfurization)
-
Ammonia and Hydrogen Reformers
-
Highly stressed locations like flanges, reducers, and pipe fittings
Key Advantages of TCR’s NDT Expertise:
-
Comprehensive assessment of long-term HTHA damage
-
Inspection over large, complex areas with external-only access
-
Estimation of damage depth without the need for equipment shutdown
​
While early-stage micro-degradation is difficult to detect, our team’s deep expertise ensures precise interpretation of HTHA in its critical stages. TCR Engineering—leading the way in safeguarding your assets from hydrogen-related risks.

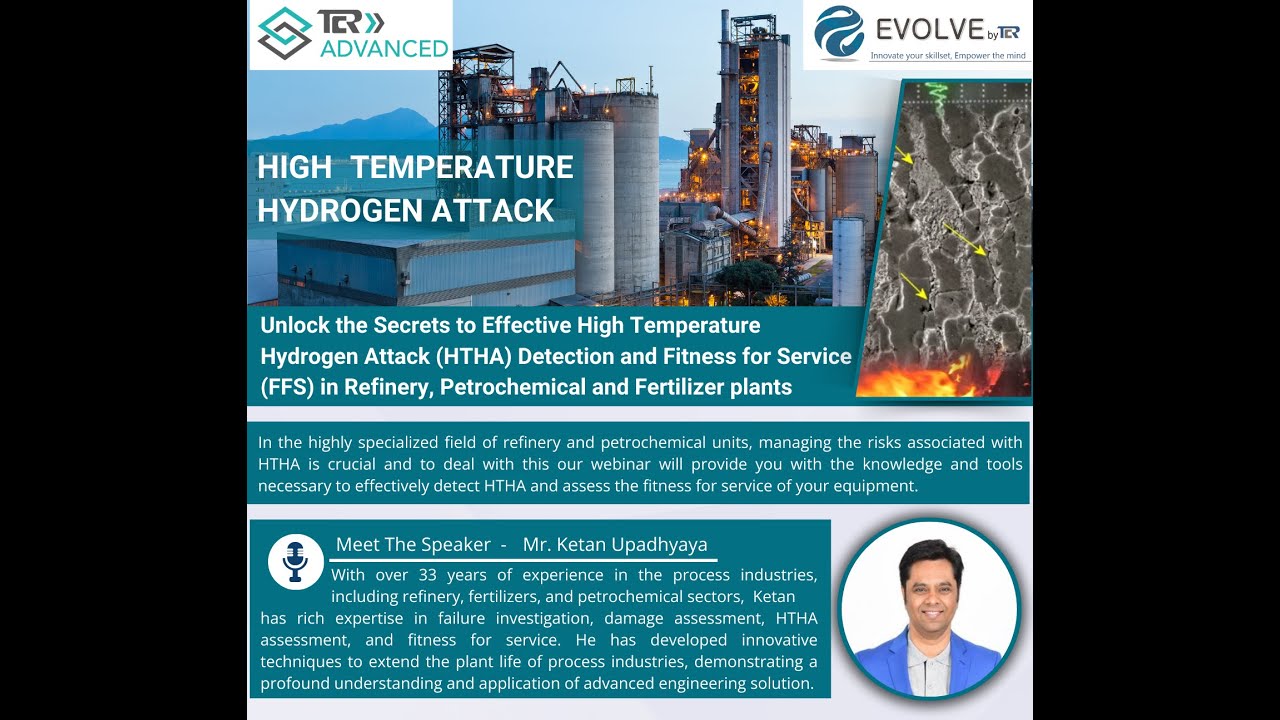