CORE SERVICE OFFERINGS
Heat Exchanger Tube Inspection
TCR Engineering provides comprehensive inspection services for tubular products using advanced non-destructive testing (NDT) methods, including Eddy Current Testing (ECT), Remote Field Eddy Current (RFEC), Magnetic Flux Leakage (MFL), and Internal Rotary Inspection System (IRIS). These techniques utilize internal diameter probe coils, such as bobbin coils, for testing both non-ferrous and ferrous materials (the latter with magnetic saturation).
Our expertise in the inspection of heat exchangers, condensers, and steam generators—commonly found in power plants—ensures the detection of critical issues like corrosion, erosion, cracking, and other material degradations. These tubular structures, which contain thousands of tubes, must be regularly monitored to prevent leaks and ensure operational integrity. The high-speed testing provided by these methods ensures accurate identification of anomalies and minimizes downtime.
The testing is conducted in accordance with relevant international standards, such as ASTM E243 for eddy current testing and ASME Boiler and Pressure Vessel Code, Section V for ultrasonic and eddy current examination of tubing. TCR Engineering’s NDT solutions ensure compliance, safety, and efficiency for critical infrastructure assets in power generation and industrial sectors.
Eddy Current Testing
TCR Engineering offers Eddy Current Testing (ECT), a fast and highly accurate technique for detecting discontinuities in tubing, heat exchangers, condensers, steam generators, air coolers, and feedwater heaters. By leveraging electromagnetic induction, TCR identifies flaws in conductive materials with precision, including detecting even the smallest cracks near the surface. This method requires minimal surface preparation and can easily accommodate complex geometries, making it ideal for a wide range of industrial applications.
In addition to flaw detection, ECT is effective for alloy separation, determining heat treatment conditions, measuring electrical conductivity, and assessing coating thickness. It can also pinpoint the location of repair welds, girth welds, and seam welds on ground-machined surfaces.
TCR Engineering’s in-house team of certified Eddy Current Testing professionals brings deep expertise in inspecting tubing in heat exchangers and other critical equipment. Our advanced testing devices are portable, contactless, and provide instant feedback, ensuring minimal downtime and maximum efficiency. Our equipment is capable of operating at frequencies up to 8 kHz, with an impressive inspection speed of 2 meters per second, ensuring rapid and reliable results.
Key Benefits of TCR Engineering's Eddy Current Testing Services:
-
High-Speed and Precise Detection: Rapid flaw identification with minimal surface preparation.
-
Complex Geometries: ECT can investigate intricate shapes and sizes.
-
Non-Destructive: Ensures the integrity of the material without physical damage.
-
Versatility: Can detect flaws, measure conductivity, and identify different alloys.
-
Immediate Feedback: Portable, real-time inspection results to facilitate quick decision-making.
Applicable Standards:
-
ASTM E243: Standard Practice for Electromagnetic (Eddy-Current) Testing of Tubular Products
-
ASME Section V: Non-Destructive Examination (NDE), covering Eddy Current Testing for heat exchanger tubes
-
ISO 15548: NDT equipment and techniques for eddy current testing
TCR Engineering ensures that all tubes are properly cleaned prior to testing, with hydro jetting at pressures ranging from 280 to 560 kg/cm². The adequacy of cleaning is verified by inserting a dummy probe or rod to guarantee smooth inspections.
Our Eddy Current Technicians expertly evaluate flaw signals generated during testing, comparing them against calibration standards to ensure the highest accuracy in flaw detection and assessment. By utilizing industry-leading equipment and adhering to stringent international standards, TCR Engineering delivers unparalleled inspection services for tubular products, ensuring your operations remain safe and reliable.

Remote Field Eddy Current Testing (RFET)
TCR Engineering offers Remote Field Testing (RFT), a cutting-edge electromagnetic non-destructive testing (NDT) method as per ASTM E2096 and ASME Section V, ideal for detecting and sizing wall thinning due to corrosion, erosion, wear, pitting, and baffle cuts in ferromagnetic tubes. Our RFT services are widely utilized in critical industrial equipment such as boilers, feedwater heaters, air coolers, and carbon steel heat exchangers, providing accurate assessments of tube integrity without the need for invasive procedures.
We combine Remote Field Eddy Current Testing (RFET) and Near Field Testing (NFT), deploying them individually or together, depending on the specific capabilities of the testing equipment and the condition of the asset. These methods allow us to achieve comprehensive coverage, ensuring reliable detection of both surface and subsurface defects.
Magnetic Flux Leakage Testing (MFL)
TCR Engineering offers Magnetic Flux Leakage (MFL), a highly reliable electromagnetic non-destructive testing (NDT) technique used to detect corrosion, pitting, and other forms of material loss in steel structures and ferromagnetic tubing. MFL is widely employed in critical industrial applications, including pipelines, storage tanks, and heat exchangers.The MFL method involves using a powerful magnet to magnetize the steel or conductive material under test. When defects like corrosion or material thinning are present, the magnetic field "leaks" from the surface, allowing our expert technicians to precisely detect and measure the extent of wall loss.
​
Key Benefits of TCR Engineering's MFL Services:
Accurate Detection of Defects: MFL is ideal for identifying sharp defects such as pitting, grooving, and circumferential cracks.
Effective for Ferromagnetic Tubing: This method is suitable for detecting defects in steel and other ferromagnetic materials.
Aluminum-Finned Carbon Steel Tubing: MFL is highly effective even in aluminum-finned carbon steel tubes, as the magnetic field remains largely unaffected by the fins.
Complementary to Remote Field Testing (RFT): MFL provides a valuable back-up inspection to RFT, ensuring a comprehensive evaluation of tube integrity.
By using TCR Engineering's advanced MFL services, industries can detect and mitigate corrosion and material loss early, enhancing asset longevity and reducing operational risks.:
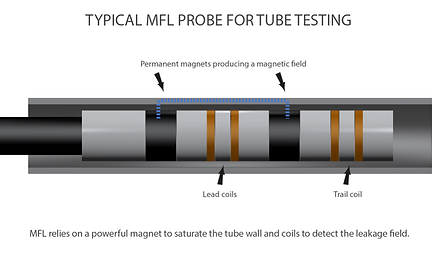

Internal Rotary Inspection System (IRIS)
TCR Engineering provides Internal Rotary Inspection System (IRIS), a highly accurate ultrasonic method for the non-destructive inspection of tubes, particularly in heat exchangers, boilers, and condensers. The IRIS technique uses an ultrasonic beam to measure and detect metal loss on both the inner and outer walls of the tube. The IRIS probe is inserted into a water-filled tube, and as it is pulled out, real-time data is displayed and recorded, allowing precise wall thickness measurement and defect detection.
Key Benefits of TCR Engineering's IRIS Services:
Precise Defect Detection: IRIS can accurately detect and measure metal loss along both the length and circumference of the tube, providing a comprehensive evaluation of tube integrity.
High Accuracy for Ferrous Materials: IRIS offers superior accuracy for measuring wall thickness in ferrous materials, with a resolution as low as 0.15mm, making it more accurate than Remote Field Eddy Current Testing (RFET) for ferrous tubes.
Comprehensive Analysis: This method is highly effective at detecting both internal and external corrosion, erosion, and other forms of degradation, making it ideal for asset integrity management.
Limitations:
Slower Testing Speed: While IRIS offers high accuracy, it is slower compared to other techniques, with a scanning speed of approximately 1 inch per second, making it less efficient for large-scale inspections.
Surface Cleaning Requirement: IRIS requires thorough cleaning of the tube surface, often more rigorous than what's required for Eddy Current Testing (ECT).
Despite its slower speed, IRIS provides unparalleled accuracy in wall thickness measurement, making it a critical method for industries focused on the longevity and reliability of their tubular assets. TCR Engineering’s experienced team ensures precise inspections that help prevent unexpected failures and extend the life of your equipment.
Fully Saturated Eddy Current Testing
TCR Engineering offers Saturation Eddy Current (SET), a specialized non-destructive testing technique used for inspecting thin ferromagnetic materials such as carbon steel (CS), duplex stainless steel, and slightly magnetic materials like Monel Nickel-Copper alloys. This advanced method is highly effective for detecting and quantifying both internal and external cracks, as well as local defects and overall wall loss in ferromagnetic tubes used in boilers, feedwater heaters, air coolers, and carbon steel heat exchangers.
This technique, done in accordance with ASTM E709. ISO 15548-1 and ASME Section V, excels at identifying both internal and external cracks, pitting, and wall thinning in challenging materials, providing detailed insights into the condition of tubes.
SET is particularly beneficial in industries like power generation and petrochemical processing, where the reliable operation of critical heat exchangers and boilers depends on early detection of material degradation.
TCR Engineering’s use of Saturation Eddy Current ensures precise inspections, enabling operators to avoid costly downtime and prevent unexpected failures.
By choosing TCR Engineering’s Saturation Eddy Current services, clients can expect high-speed, accurate inspections that extend the lifespan of their critical components, ensuring operational reliability and safety.